Noise and Vibration
Background
Railway operational noise originates from a number of sources.
- Engines and cooling fans of locomotives,
- Under-floor engines of “diesel multiple units1” (self-propelled sets of railway coaches)
- Gears
- Aerodynamic
- Effects at higher speeds
- Interaction of wheels and rails (influence on overall noise levels at speeds above 50 km/h
Noise is normally predominant at speeds above around 100 km/h). Wheel/rail noise, or “rolling noise”, results from the vibration–excitation of the wheels and track as the wheel rolls on the rail. The excitation is provided by the combined surface roughness at the interface, or “contact patch”, between the wheel and the rail. Because the entire wheel and track system is excited by the combined roughness at the interface, it is this combined value that determines the level of rolling noise rather than the individual rail and wheel roughness components. As noise levels increase with growing corrugation depth the intervention threshold is often set at 0.05 mm peak‐to‐peak depth for short pitch corrugation, which also helps to minimize dynamic forces as track vibrations start to damage the ballast structure at that level and to reduce the risk for subsurface initiated RCF of wheels and rails.
Roughness of the rail head can influence the level of rolling noise.
The rail head will normally exhibit a “broad-band” surface roughness but at some locations there are periodic wear patterns, known as corrugations, which can have significantly greater amplitudes than the general broad band roughness. Where wheels are comparatively smooth, the difference between rolling noise on smooth track and on badly corrugated track can be more than 20 dB(A), an approximate quadrupling of perceived loudness. As well as the acoustic implications, corrugations will increase the forces on track components and, in severe cases, can interfere with the coupling of ultrasonic transducers with the rail when non-destructive testing is being carried out. For both the wheels and the rails, the wavelengths of surface roughness of particular relevance to rolling noise are between 5 and 200mm, although there is a filtering effect for shorter wavelengths at the contact patch due to its size (typically 10-15mm long). The frequency of vibration excited by the roughness is simply related to the roughness wavelength by the equation: Frequency = Velocity/Wavelength. To illustrate this relationship, roughness wavelengths of 20mm and 200mm will generate a vibration excitation at 1400 Hz and 140 Hz respectively at 100 km/h. Rail and wheel roughness spectra are normally presented in terms of roughness expressed in decibels vs wavelength. Roughness in decibels relates directly to the unit used to quantify sound, and allows a certain degree of immediate interpretation by the experienced practitioner. This value is obtained from 20 log10 ([root mean square roughness amplitude]/[root mean square reference level, normally taken as 1 x 10-6m ie 1 micron]). Using this decibel scale, a roughness value of 1×10-6m = 0 dB, 3.2×10-6m= 10 dB, 10×10-6m= 20 dB etc.
Difference between “squeal” and “Flanging”
“Squeal” dominated by a single frequency, generally above 1.5kHz, which is typically more than 20dB above the rolling noise level. “Flanging” is the multi-modal rubbing noise generated by contact between the flange of the wheel and the gauge face of the rail. It is often well above the rolling noise level too, but in our experience is not nearly as loud as squeal and hence is less annoying for residents near rail lines. It is important to first identify noise sections and offending components in order to manage them.
Vibrations
Train generates vibrations which are transmitted through the track to the ground, resulting in vibration and re-radiation noise in nearby building. The amplitude of vibrations depends on several factors, such as roughness of wheels and rails, dynamic properties of a train, a vehicle speed, characteristics of a railway track, a soil damping and a propagation of waves thought the soil. Vibration can be measured on train body and on track at the same time. On train Vibrations were analyzed in terms of accelerations, velocities or displacements as a function of time and frequency. The displacements were obtained by double integration of acceleration results. The traditional approach to measuring noise and vibrations is through setting up specific experimental data recording sites along the track as shown below. Such approaches are expensive and do not give proper information on all track sections where noise and vibration are issues.
- It is very difficult to determine exact locations where vibration, and noise should be measured
- Only limited sites can be used in the study
- Identification of offending wheels is error prone
- It is not possible to generate a complete repository of the behaviour of each wheel against their movement on various track sections
RV Diagnostics
Our diagnostic systems for noise and vibration measurement are mounted on the vehicle as opposed to trackside, ideally close to the source of noise and vibration, e.g. bogie. TrackVue R series products for on-board condition monitoring are ideally suited for noise and vibration measurements. The systems record noise and vibration data in terms of amplitude and frequency and transmit alerts to a command centre on track positions where the recorded values are above set thresholds.
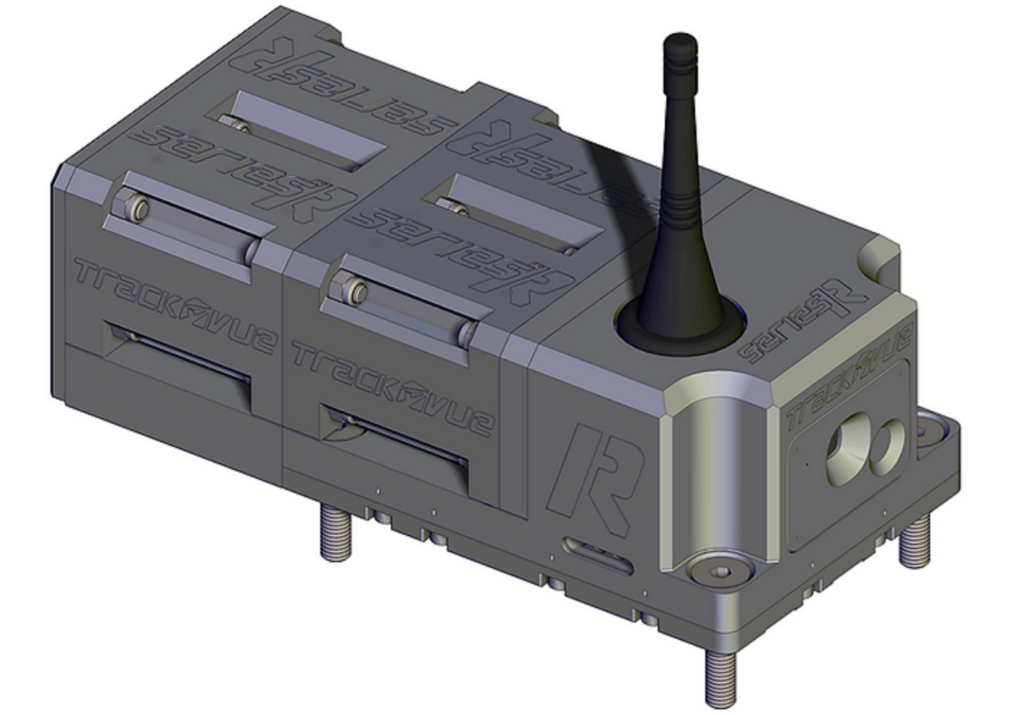
TrackVue Series R On-board Condition Monitoring based Sensor Network Units are placed on each bogie to record noise data. The system also measures vibration if attached to the vibrating surface. For axle and pivot based accelerations a separate measurement device is used. This unit is completely battery operated and sends all alarms for noise and vibration to a cloud server from where users can see the condition of each wheel set.
These units can be programmed to record certain frequency noise and vibrations to filter data of interest and are ideal for recognising wheel squeal and noise and vibrations coming out of broken or malfunctioning units.
The sections of track with excessive noise and vibration issues are highlighted on track layouts as shown below.
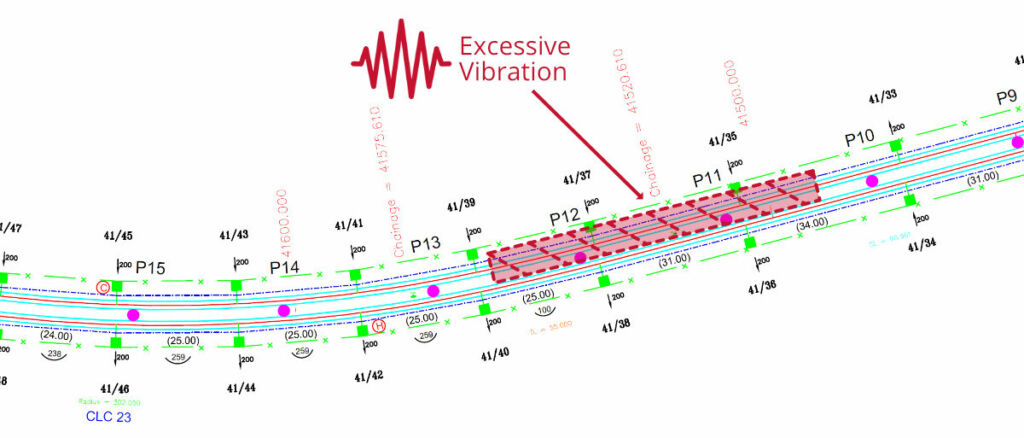
We use the following approach to noise and vibration management using our sensor based analytics.
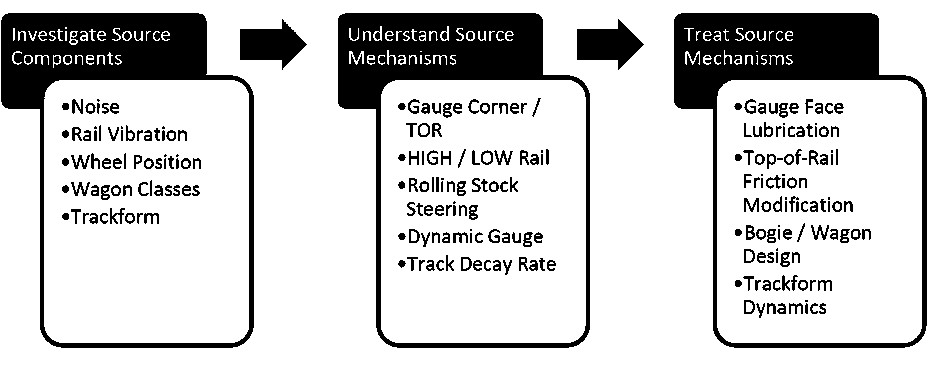
RV Advantage
- We are one of the very few companies using patented sensor networks to make such measurements. These can be made continuously as opposed to on specific track sites.
- We try to understand the root cause behind noise and vibrations as shown below and offer consultancy to operators on how to solve the problem