Personal Safety
Background
The personal safety of passengers when boarding trains is extremely important. Modern day railways stations are no different to airports whereby all luggage carried by them must be scanned. Train stations and trains can be potential target for terrorists and it is also a conduit for smuggled goods. Dual energy x-ray systems have long been used in airports and other establishments and were the first choice for all rail stations to adopt. Unfortunately, train and metro stations do not exactly operate like an airport. Passengers do not need to turn up much in advance of trains departing and in many countries is not still not needed to have personal identification checks to board the train. For mainline railway stations, people and their luggage may generate large queues just before trains leaving. If the luggage inspection system is not high speed, passengers may not be able to board their reserved trains and may have long waiting times. In case of metros, trains are more frequent but Metro stations are usually more compact and long queues are not ideal. Therefore in both cases, we need a high speed luggage inspection system. Human screening of data is a major bottleneck where scanning one passenger may take at least 10 seconds. Recently, some metros have started to adopt higher speed x-ray scanners. These scanners will now be capable of handling up to 550 bags per hour which used to be around 350 bags per hour earlier. For this, the conveyor belt speed has been increased from 18 cm per second to 30 cm per second. This is intended to reduce the heavy passenger rush at the frisking points especially during peak hours however safety concerns remain; shortening inspection period will lead to a less reliable system.
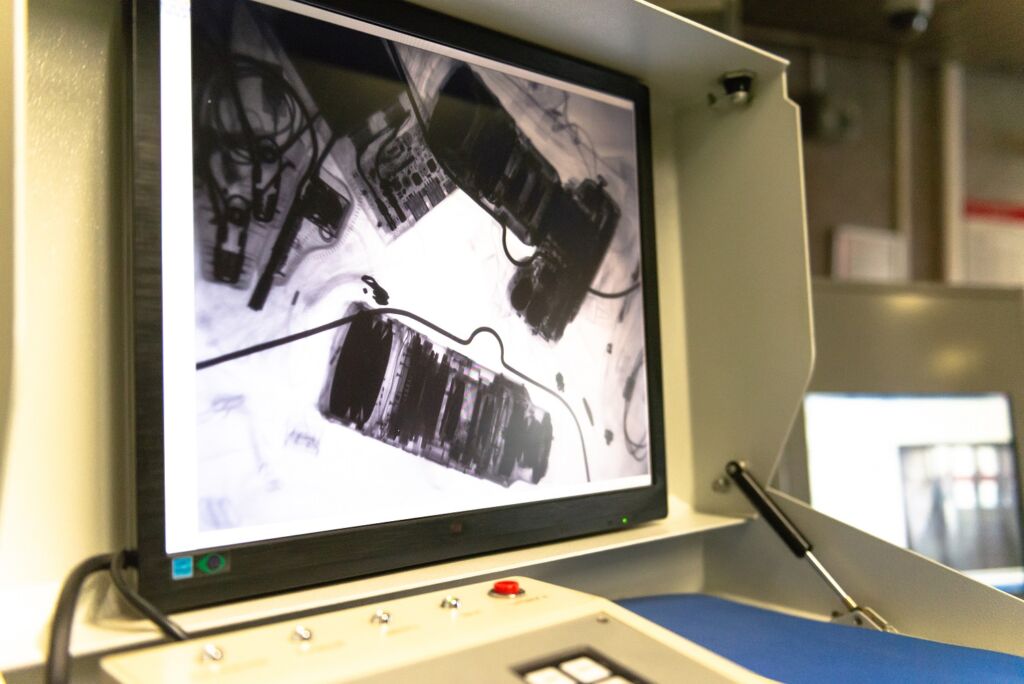
SafetyNET
Rail Vision product SafetyNet is designed to turn any scanner into a smart scanner. It provides an option to either fully automate luggage scanning which is capable of handling more than 2000 bags per hour with appropriate conveyor belts, to providing a hybrid inspection system where SafetyNet provides a second layer of checking beyond human screening to improve performance. The following image shows a SafetyNet device which contains a processor and AI based data analytics software to take a copy of image data seen by the human operator and to process it to generate alarms where present.
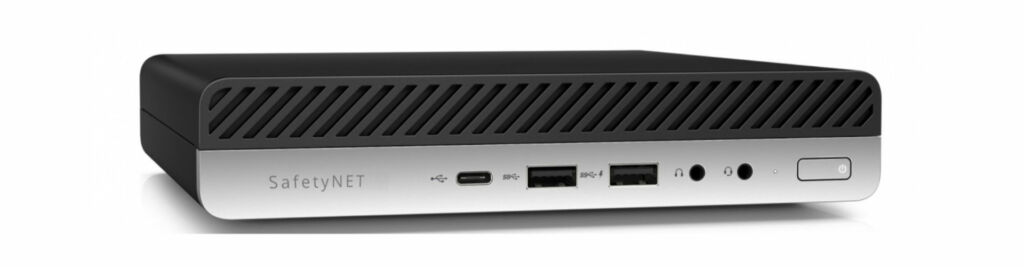
The system interfaces with a range of x-ray scanners provided by various leading vendors without any major hardware of software modifications to these scanners and is able to screen for threats in less than 100msec. The following image shows how this approach provides a SafetyNet around human decision making.
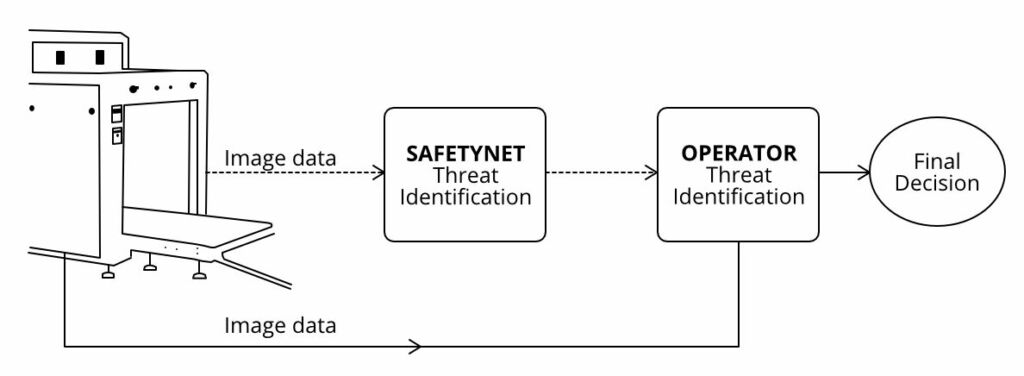
RV Advantage
There are several drawbacks to relying on human visual system alone for interpreting screening images.
- The first drawback is that scanned image data is often relatively complex as the radiation is not able to penetrate through high density material. A complex assembly of goods in a container, luggage, parcel or very well concealed items on a person can manifest as a fairly complex image. In many cases, poor image contrast resulting from limitations of radiation imaging can produce images where objects are hard to discriminate. Several objects may be on top of each other, obscured, deliberately hidden and can have variable appearance based on their orientation with respect to the sensors. The human visual system may not be able to discriminate and comprehend the most complex images which are most likely to contain objects of interest for further interrogation.
- The second drawback is that the human visual system is put under stress because of limited time allowed for checking a single piece of cargo, luggage, parcel or person. In a typical x-ray luggage screening system, the operator has less than 6 seconds to evaluate the baggage. The actual time available is reduced because of a rolling image that builds up similar to a linescan system, and therefore the operator may see the entire object image for a short period. Extending inspection time may lead to backlog building up quickly. Visual fatigue can further reduce performance levels.
- The third drawback is the monotonous nature of work that can affect human operator performance. Radiation based sensor imaging produces images with limited number of colours and often leads to visual fatigue if such data is looked at for long periods of time. For this reason, screening operators work in shifts to minimize visual fatigue. It is well documented that long periods of work on this type of data reduces performance and concentration levels.
- The fourth drawback is the variability and level of operator training. The level of training of human operators and their level of expertise is highly variable. This means that the quality of screening is more dependent on the screening operator rather than the machine itself. The repeatability in performance and correlation in quality of performance can be poor across different operators. This poses a serious risk to the overall quality of screening and decision making for such applications.
SafetyNet addresses all of these drawbacks. Some of its key strengths include:
- SafetyNet provides a second level screening layer without disturbing the current practice of how human operators screen scanner data.
- SafetyNet is implemented as a singular assembly device containing computational resources including computer processor, clock, embedded electronics, data storage and other components that allow images to be received from the screening machines through SafetyNet interface, to be processed, locally stored, tagged with time and operator data, and for results to be relayed to the SafetyNet console. Each image received by the processor is analysed in less than 100 ms such that the results are instantly available for further use. The processor can be positioned in close proximity of the screening machine such that interfacing is convenient.
- SafetyNet algorithms are implemented on the processor and are modular in nature. Separate modules related to image enhancement, threat detection, self-learning and so on are available. SafetyNet learns from experience and ground-truthed image data. Initially, a large number of image data is ground-truthed for threat and normal conditions. Artificial intelligence algorithms use such data in a variety of supervised and unsupervised paradigms along with embedded intelligence in image analysis.
- Image analytics algorithms work on two and three dimensional image data. This allows for SafetyNet to be used for three dimensional CT scanners.
- SafetyNet has a cloud interface that helps identify which operators need further training.