TrackVue V Series
Complete catenary measurement solution
V series product focusses on overhead line based inspection. In addition to monitoring standard OHE parameters, it also provides a indirect measurement of pantograph dynamic forces calculated using video analytics which provides a simpler approach compared to instrumented pantographs. System output includes:
- Catenary wire based measurements for loaded and unloaded sections
- Contact wire height, width and stagger, wire thickness in mm with 0.5mm accuracy
- Pantograph contact position, deviation over time, contact temperature, arcing, dynamic vertical movement
- Catenary mast evaluation, their positions, transformer condition, thermal condition of insulators, wires, contacts, and visual condition (broken and missing components, surface condition (e.g. snow, rust)
- Animation and virtual reality models
TrackVue V product series measures various overhead line (catenary) parameters. The equipment is mounted on top of the inspection vehicle. It consists of camera (optical and thermal) and 3D laser profiling equipment. Its main features include:
- Colour areascan camera options, resolutions of 8Mps and above, sampling rates between 25 fps to 120 fps
- Inertial sensors of tactical grade
- Pantograph, catenary and side view (overheads masts) camera views
- Dynamic exposure adjustment to image in variable weather conditions
- Thermal cameras for arc and temperature measurement, 7.1 Mps, 60 fps
- 3D Laser profiler for measuring wire thickness and other parameters
- Laser data acquisition every 20 cm, class 3B, working range 120-470mm
- IP67 or higher rated; 1 Gb Ethernet interface
- Operational Voltage: 24VDC
- Typical power consumption 5kW
- 48Tb+ on-board storage
- Dedicated management software
- 24/7 all-weather all-time operation
- Remote operation possible
- On-board real-time data analysis for critical issues
- Offboard data re-processing available
- Sub-ambient liquid cooled for high performance in hot countries
- Full data management services including option to use cloud interface
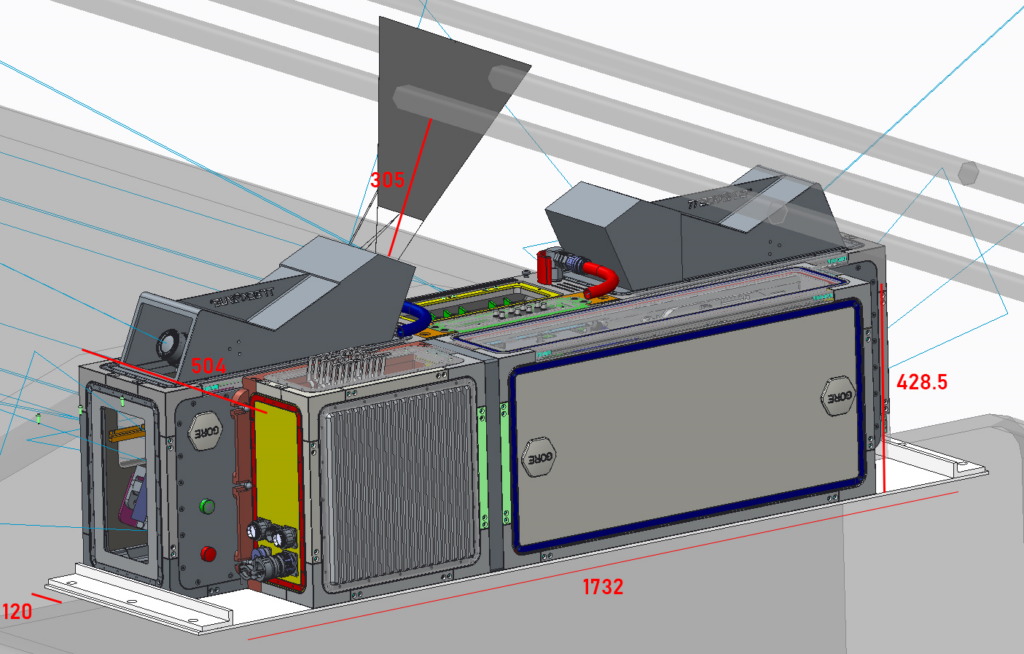
TrackVue V series equipment is designed to work in sunlight and in a variety of weather conditions. Sensors auto-adjust their exposure and sampling rate to ensure that good quality data is sampled at fixed intervals irrespective of time of the day or weather conditions. It has a compact design and can be easily positioned 5-8 meters away from the pantograph. A simpler video inspection system for monitoring pantographs only is also under development that will have a very compact form factor for imaging pantograph movements and will mimic the measurements made by an instrumented pantograph on dynamic forces between pantograph and contact wire. Environmental protection of equipment is very important for V series as it is directly exposed to rain, sunlight, bird droppings and dust.
TrackVue V Series equipment is designed for the diagnostics of overhead catenary wires and their support infrastructure such as masts. Determining position of the contact wire with respect to track centreline is important. The contact wire runs in a zig-zag path above the track to avoid excessive pantograph wear. The zig-zag pattern known as the ‘stagger’ is generally achieved by the use of ‘pull-off’ arms attached to the support structures. Stagger data can be thresholded to determine exceptions or abnormal stagger. The height of the contact wire with respect to a fixed point in space such as rail level is also important to measure to determine current tensioning levels. Reduced height because of wire sagging or incorrect tensioning can lead to abnormal pantograph contact and damage to both the wire and the pantograph. The thickness of contact wire must also be measured as decrease in diameter is an indicator of stressed wire that may break over time. In addition to these three critical parameters, various other features of pantograph/contact wire interface can be measured such as chipped or damaged insulators, condition of steel wire ropes, displacement of tensioning equipment, rusted parts in cantilever assembly, displaced fittings, damaged droppers, etc.