Condition Monitoring
Background
The condition monitoring of assets with drones is much more challenging compared to train-borne systems for a variety of reasons. With train-borne systems, power, space and trajectory of inspection is fixed and sufficient, i.e. inspection equipment can take power directly from the train, can be mounted in a variety of positions and the positioning of sensors with respect to the track centreline is fixed. This is not true for drones. The flight path is difficult to be very precise from run to run, the load carrying capacity and power limited, and depending on where the drones are allowed to fly to avoid collisions, the angle of viewing and distance to objects may not be as consistent as needed. This generates a more complex set of imagery and 3D measurements for AI based analytics to deal with. As electronics continues to be miniaturised, the resolution of sensors mounted on drones will get higher which can be stored on SSDs and transmitted with 5G technology. Despite this, the data analytics processes and algorithms for drone data are more advanced and complex than train-borne systems. The automated detection and recognition of objects and context, to zoom into measurement areas, remains a challenge. Without analytics automation unfortunately drone data is impossible to manage; a short drone run can create gigabytes of data.
Drone based inspections are usually fixed around a central asset that needs to be inspected, or may be carried around on a fixed flight path where larger distances are involved. In all cases, drone position is controlled and in sight such that any collisions can be avoided and all required areas can be inspected. Railway infrastructure provides a challenging environment for the drones. The following assets provide a natural ground for aerial inspection.
- Overhead lines, measurement of sag and geometry
- Bridges, detection of visual defects, cracks, missing fastenings, rust areas, track layout and condition in bridge sections
- Tunnels, 3D mapping and clearances
- Vegetation, clearance to overhead lines, vegetation mapping
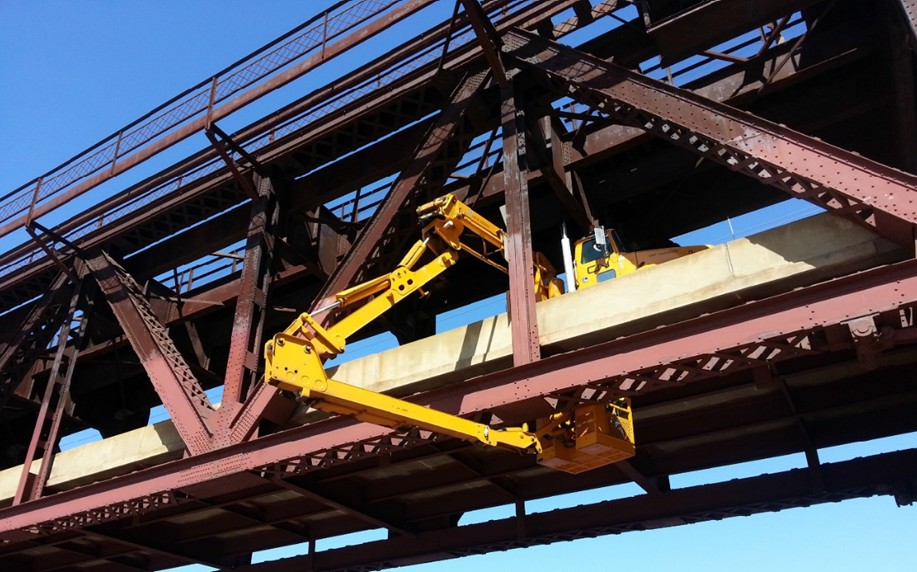
In each of these areas, performing manual inspection is difficult, time consuming and does not provide the same view as drones are capable of giving. In several cases, it is also very hard for human inspectors to image certain assets such as bridges because positions can be at a height and dangerous, and special climbing staff or trolleys to carry people are needed. Drones can collect a lot of data in such cases with very little effort however the data variability is enormous compared to data collected from train-borne systems where sensor geometry with respect to the track is fixed. Rail Vision has expertise on such data and its automated analytics using AI based machine vision algorithms.
RV Diagnostics
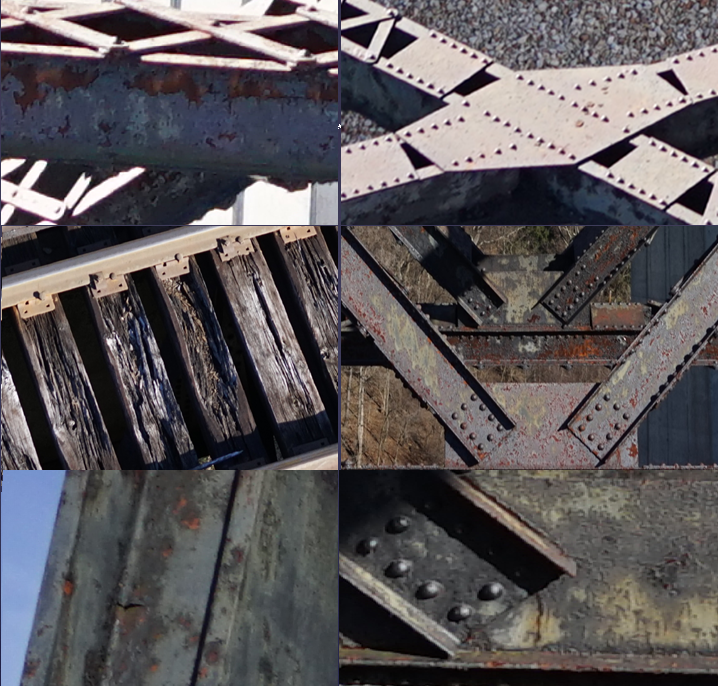
The image on the left shows a range of defects found by our system on rail bridges. The drones can fly fairly close to the asset under inspection and manoeuvre in tight spots. The images show cracks on steel beams, rusting, chipping, broken sleepers and small detached components. A key part of the diagnostic is to clearly label with respect to the bridge, where defect has been found. To do this, the drone records its GPS and post-processing uses survey CAD diagrams of the bridge to highlight point of defect / region of interest. The data is transmitted to our RV Cloud facility that provides a front-end for the customer from where they can download reports and view video and image footage showing the defect. The defects are automatically measured for dimensions in mm. Maintenance prioritisation is performed by infrastructure owner. For bridges, a number of faults can be determined using drone images including Top of deck faults, Prestressed concrete girder or beam defects, Floorbeam defects, Column defects, Abutment defects, Pier Cap defects, Strip Seal Deck Joint defects, Elastomeric (Expansion) Bearing defects, Fixed Bearing defects, Masonry, Other or Combination Material Railing defects.
RV Advantage
Rail Vision has an edge over competition on drone based solutions for the following reasons.
- Our technology is not tied to any specific drone or sensor
- We have the most experience of any other competition on vision based data analytics for unstructured environments which requires sensor combination and high level of expertise in scene understanding
- We are working on Innovation Agenda to solve some fundamental issues that will see the application of drones to a broader range of applications in railways. Beyond Line of Sight (BLOS) and use of AI Chips for on-board real-time data processing are two of those key developments that will be tried for railways.
- Our data analytics is automated which can be scaled up easily for more data by using more processors as opposed to manual which will struggle even with small amounts of data.