Vehicle Undercarriage Diagnostics
Background
Rolling stock undercarriage inspections are typically carried out manually whereby all vehicles returning to a maintenance depot are inspected for obvious faults. This is a tedious task for people to go under the vehicle and use basic tools to check for obvious problems that can be visually seen, e.g. completely broken components, oil leakages, heat damage, etc. Separate teams may be assigned for manual measurements with handheld tools, for example, wheel wear measurements. Such an approach is slow, infrequent for each vehicle, and does not diagnose problems in their early stages. It does not generate any data which may be historically kept for each component for its predictive maintenance. Furthermore, outside of planned maintenance checks, diagnosis is only possible once the vehicle has a critical failure and it returns to workshop. Ideally, it would be useful to have this diagnostic facility for vehicles in outdoor areas where vehicles run with full line speed and inspected with sensors from underneath, such that any critical defects can be immediately communicated to the driver and operational command centre.
RV Diagnostics
RV TrackVue R series wayside solution places equipment under the vehicle to inspect the passing vehicle above at full line speeds. The sensors are so placed as to inspect a broad range of faults as shown below.
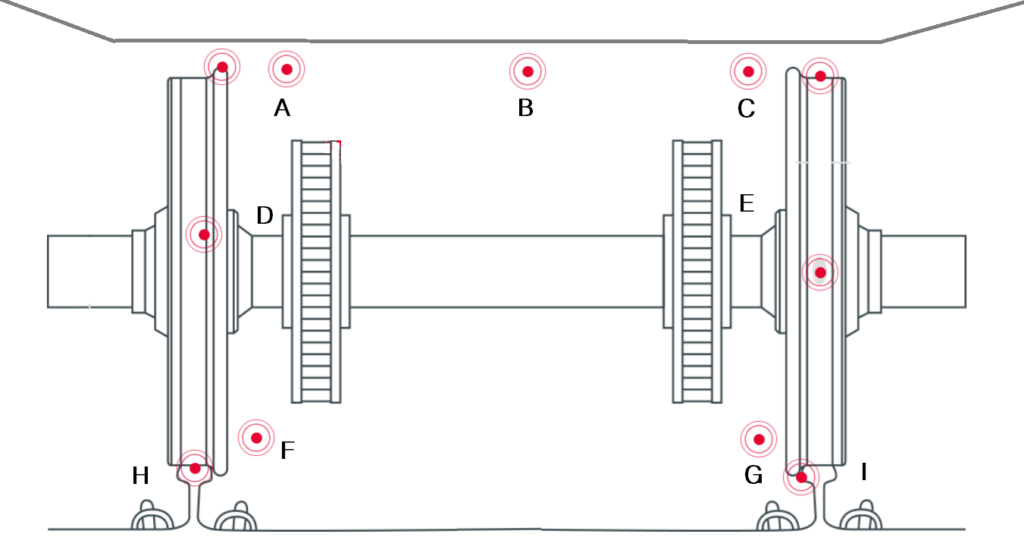
The area under the vehicle often has a different layout for different vehicle designs and a CAD drawing of the design is used alongside AI algorithms to diagnose specific components. Linescan, laser, acoustic and thermal sensors are used. All analysis is indexed for vehicle ID, coach/railcar ID, component ID, and position of defect relative to the coach start. It is important for the system to report missed measurements where the component of interest is obscured from view.
Areas A, B and C represent the under-carriage areas where we can determine the following faults with the correct equipment:
- Visually detectable structural integrity defects like cracks etc. of underframe, as visible from ground below the underframe between the tracks.
- Yoke pin support plate bolts missing or broken for CBC stock
- Damaged Centre sill or other under frame members as visible to the human inspector’s naked eye
- Missing CBC knuckle pins
- Missing CBC operating handles
- Damaged/broken Empty Load devices
- Missing Brake gear items
- Broken or Bent Brake beams
- Missing/damaged brake pipe hose/feed pipe hose
- Hanging parts
Furthermore, it is important that both wheel hub bearing area and undercarriage area must be inspected for abnormally high temperatures that indicate faults.
Areas D and E are of interest for analysing wheel bearings. Areas of side defects of interest include.
- Broken / Missing Axle Box covers
- Major damages in Wheel Disc
- Open/hanging Doors of Wagons
- Laterally displaced Springs/ Shock Absorbers, as applicable
- Standard Wheel Profile and other wheel related defects (hollow tyre, deep flange, thin flange, difference in wheel diameter of the same axle etc.)
- Brake pads/ brake block Worn or missing
- Broken or missing Brake beams and pull rods
- Broken or missing suspension springs
- Missing/ Damaged Springs
- Missing Brake Block or key
- Missing/ damaged hand brake wheels
Areas F and G are of interest in determining wheel parameters. These include wheel diameter, and wheel profile data measured at various points on wheel surface as shown below. A laser based device is employed to measure the tread measurements using laser rail profile. Currently such measurements are made by handheld tool sold by Calipri which will become obsolete once automated methods such as ours are implemented. A separate section on the website dealing with wheel diagnostics shows the wheel profile and areas of the wheel where measurements need to be made to check on wear and current wheel diameter.
Furthermore, additional devices are needed to measure rail wheel interaction at points H and I in the above figure. A different piece of equipment called TrackVue Z series already exists to make such measurements.
The following image shows a concept drawing of how TrackVue series R equipment looks with various sensors. The equipment comes with its own dedicated LED lighting to light the underside of the train. It comes with a protective rugged covering assembly to keep out dust and water, which is automatically removed once the train is arrived and the system starts to capture data. All sensor analytics is tagged for time-stamp and indexed against details of the vehicle, coach/railcar and position of the defect.
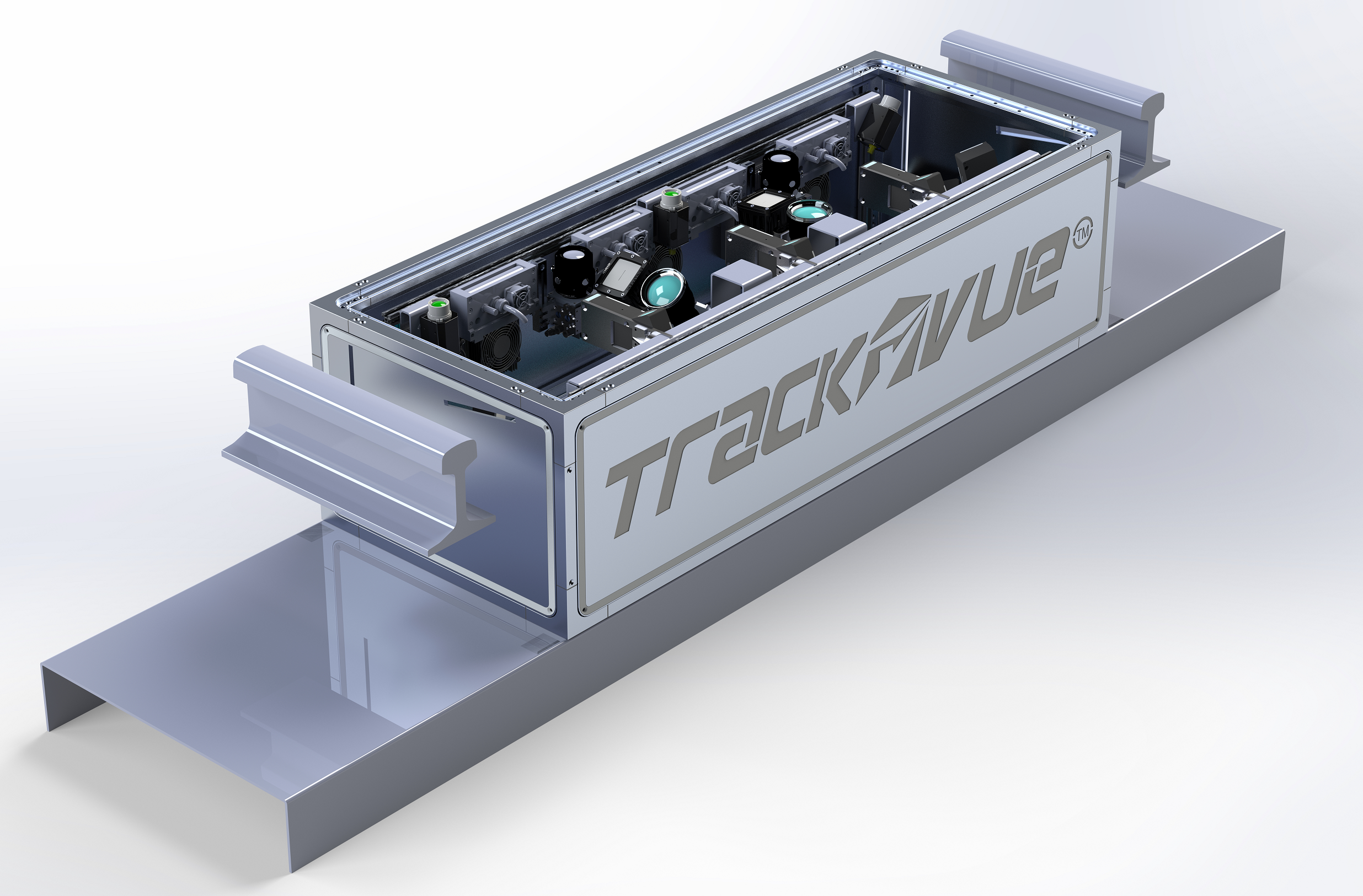
RV Advantage
- There are several benefits of the TrackVue R series equipment over limited number of existing solutions to undercarriage monitoring. These include.
- We provide a single piece of equipment to both perform undercarriage monitoring and wheel diagnostics (wear and diameter measurements)
- The system comes with integrated LED lighting and filters sunlight, and therefore it can be used both in workshop and out-in-the-field environments
- All measurements are made in real-time and transmitted with image evidence to a command centre and cloud server
- We provides a wider range of detection facility by covering lateral end-to-end of the rolling stock body to image all elements and can place thermal sensors on objects of interest