Bearings Condition Monitoring
Background
Train accidents are often due to worn bogie parts (wheels, axles, brakes & bearings) overheating, breaking, & derailing the wagon affected. Axle failures cause 51% of derailments in the EU & 11.1% in the USA as per research. To identify this heat, Hot Axle Box & Hot Wheel (HABD/HWD) detection units are mounted at the track side. HABD/HWD use infrared (IR) sensors to makes point based measurements of passing bogie IR radiation, which is converted into electric voltages & displayed as absolute temperatures. There are limitations with HABD/HWD, such as sampling of incorrect target points giving inaccurate information, as well as detrimental effects from solar radiation. HABD/HWD measure the temperatures of bogie parts using infrared (IR) beams which detect temperatures 0-650°C. The IR sensor makes point based measurements of passing bogie IR radiation, which is converted into electric voltages & displayed as absolute temperatures.
There are limitations with HABD/HWD: each is factory-calibrated against a standard bogie; in real-world settings, there are many different bogie configurations, which coupled with variance of wheel position measurements lead to sampling of incorrect target points, giving inaccurate information. Also, if excessive heat related failure develop in areas with no HABD/HWD trackside installations, or between two installations, preventive action cannot be taken. HABD/HWD measurements can also be detrimentally affected by solar radiation reflection onto parts of the train, braking sparks, & disturbing heat sources in or near the area of the measured surfaces. The following image shows disastrous consequences of not detecting bearing failures in good time leading to a complete burn and melt down of various wheel components.
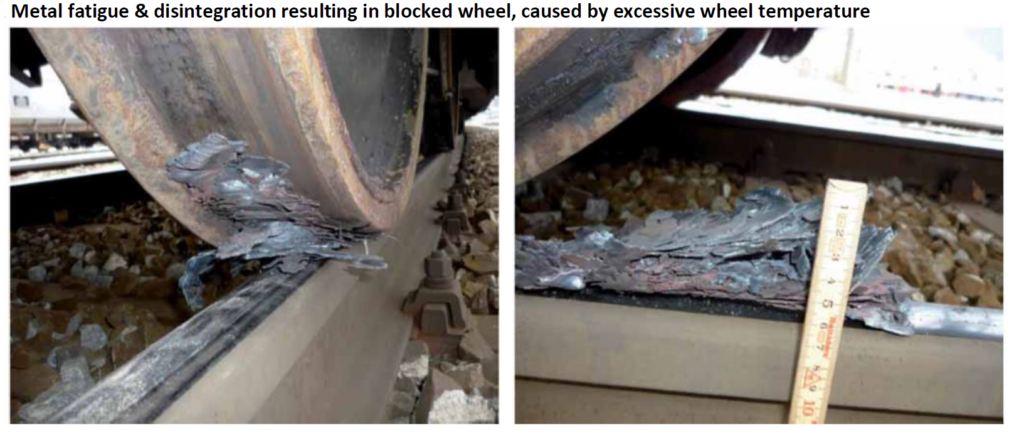
It is clear that the use of wayside Hot Axle and Hot Wheel detection systems have limited future potential given technical issues. An on-board condition monitoring device that is able to monitor bearings continuously is needed. The sensor device will be mounted on every bogie and create a sensor network on-board the train to move measurements from point of capture to a centralised cloud database.
RV Diagnostics
TrackVue R series On-board Condition Monitoring System is the perfect choice for monitoring rail bearings. This is a contactless system that uses 3 types of sensors within an integrated platform. These include:
- Thermal sensor, to monitor the rise in temperature of the bearing compared to the ambient temperature, which can be thresholded to generate exceptions
- Acoustic sensor, to monitor the various frequencies present in the acoustic data to identify abnormal sounds that represent bearing failure
- Vibration sensor, to monitor the vibration levels at the position where the device is installed.
The device therefore combines the functionality of a Hot Axle Box Detector and a Acoustic Bearings Detector along with vibration detection. The overall system consists of a number of monitoring devices, each mounted on the bogie or surround areas as needed, where the thermal sensor is directly pointed to the bearing position. These network of devices use their own data transfer protocol to message bearing failures to a central computer on-board the train, the informs the driver on critical failures and relays the information to an operational command centre and feeds a cloud based server.
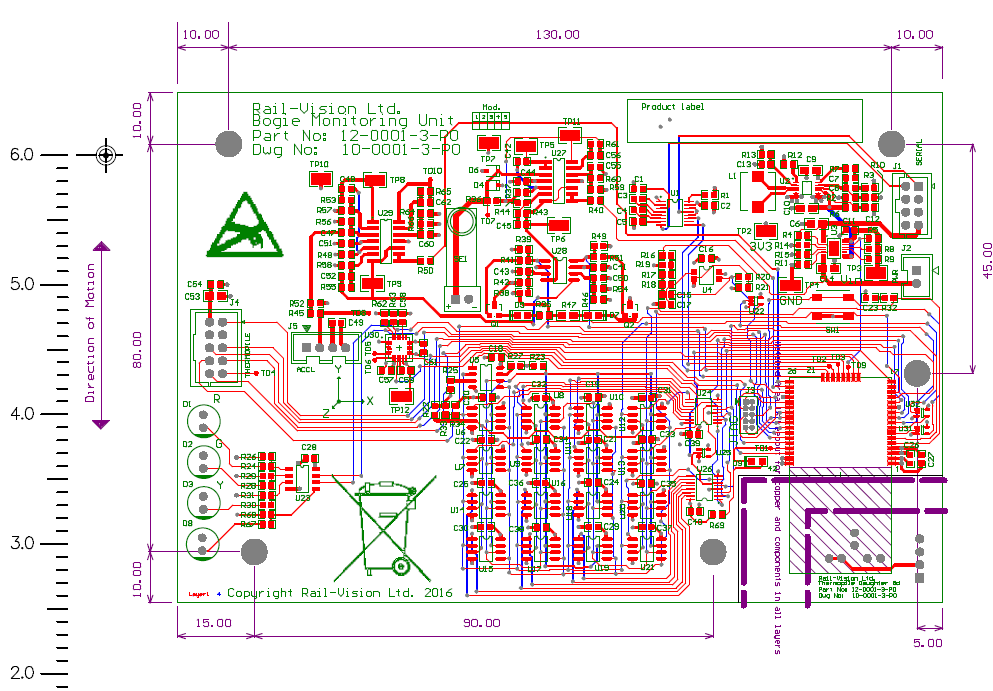
The heart of the TrackVue R series on-board condition monitoring device is embedded AI based decision making circuit board that uses all input data from various sensors and analyses these further to identify key failures. This patented technology uses signal data as input, applies a range of advanced AI based signal processing techniques to filter signals of interest, and makes a diagnosis on bearing condition by combining thermal and acoustic information. The system samples the wheel every 1 minute initially on start-up and much more frequently if measurement parameters show an increase in activity that points to potential bearing failure. The circuit and sensors are low-power consuming components allowing the system to work for up to 2 years without any battery changes.
Our system works on the data with advanced AI based signal processing methods to perform adequate noise reduction, filtering and spectral analysis in chosen wavebands to determine defects as they arise. Measurements made include:
Bearing measurements | |
---|---|
Temperature | Max, Average in Celsius across a chosen cross-section areas measured at set sampling rate continuously |
Acoustic | High frequency signal analytics with calculation of maximum energy concentrated in chosen frequency bands, exception thresholding in each band of interest |
Vibration | Spectral analysis parameters at various vibration frequencies, filtering data within specific frequency bands, correlation with vehicle dynamics data (acceleration and gyro rates in 3D) |
RV Advantage
- Rail Vision’s TrackVue R series devices provide a number of advantages for bearing defect detection as detailed below.
- Wayside devices are no longer needed. A more accurate set of diagnostic data is available continuously for all wheels inspected.
- The system integrates various technologies in one devices such as thermal, vibration and acoustic giving a complete data set for full bearing review. This eliminates the need for different methods of measurement as separate devices.
- The devices can be retrofitted to any vehicle giving them maximum flexibility of usage.
Bearing faults are detected and reported in real-time. - The sensing device is non-contact and can be positioned roughly 20-30 cms away from the target.
- A web-portal delivers customer data in close to real-time showing vehicle position on track, and condition of each bearing on a chosen scale.